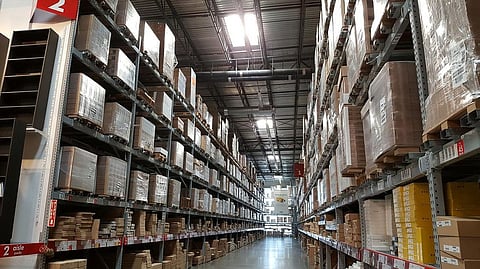
The core of any retail, manufacturing, or logistics business is the efficiency of its warehouse system. This goldmine can spell the difference between gains or losses. A business transaction does not solely revolve around a physical store or an online shopping portal. It relies heavily on the warehouse and its capacity to protect the products at all times.
You may be a startup that wants to transition from your garage to a full-scale warehouse. Or you may be an existing business owner who wants to increase productivity. When you have efficient and effective warehouse racking systems, you will have an ally that can help make your goals into a reality.
Here are six factors to ponder about when choosing the best warehouse racking system for your business:
You may be a startup that wants to transition from your garage to a full-scale warehouse. Pixabay
Selectivity refers to the accessibility of the products from the shelves and racks. If your company has a wide variety of products that need to be distributed immediately, choose a system that has easy access. If there is a need to access specific boxes, pallets, or bins several times in a day, avoid additional labor by using single depth racks. This kind of rack prevents other pallets from being "buried" at the back.
In logistics parlance, density is the storage capacity per cubic meter. Bear in mind that an increase in density means a decrease in selectivity. Manufacturing plants that have a production line for the same product need warehouse racking systems that have a higher density. This type of business requires quick and massive storage capacity, rather than the accessibility of the products. The best kind of system would be double or triple depth racks.
Recommended for operations, pallet flow racks require the First-In-First-Out environment. Note that boxes or bins that get buried at the back may increase the effort and cost of handling. Consider the flow of the inventory before making any decision.
Not all boxes, pallets, or bins have the same shape or size. Check the packaging of both your products and the suppliers'. Inconsistent packaging may require additional accessories like rack decking or pallet support to ensure the safety and stability of the racking system.
Or you may be an existing business owner who wants to increase productivity. Pixabay
Picking profile introduces the process of getting the products from the shelves or racks to fulfill customer orders. It determines how the products will be accessed. Will they be picked per pallet, per case, or per piece? This information will have a significant effect on the type and configuration of the racking system that the business requires.
Research on the Federal state and local codes regarding seismic codes before you plan the racking system of your warehouse. Check if the business' location belongs to a seismic zone. It means that the area is more prone to earthquakes. Therefore, it's vital to install a stricter warehouse racking system. The law will require sturdier engineering of humanmade structures such as shelves and racks.
Also Read- Steps in Getting a Medical Marijuana Card
Before designing a warehouse system and purchasing the needed materials, a business owner must evaluate the company's needs and goals. Each factor must be included to maximize the investment and effort in putting up one of the most critical areas in a business. An efficient warehouse system will be your partner in business growth and success.