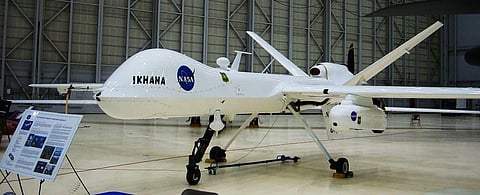
Washington, November 4, 2016: A team of NASA researchers and students is using emerging composite material manufacturing methods to build an ultra-light wing that actively changes shape to help reduce fuel use and improve flight efficiency.
Increased efficiency means less fuel is needed, which means less weight on the aircraft, which also increases efficiency.
NewsGram brings to you current foreign news from all over the world.
This "holy grail" of more efficient flight is always in the minds of the Mission Adaptive Digital Composite Aerostructure Technologies, or MADCAT, team at NASA's Ames Research Center in California's Silicon Valley, NASA said in a statement on Thursday.
The ultra-light wing that actively changes shape could be an important part of the future of green aviation, said Kenneth Cheung, co-lead on the MADCAT project.
This type of wing could improve aerodynamic efficiency in future flight vehicles by reducing the amount of drag caused by rigid control surfaces like flaps, rudders and ailerons.
Earlier studies of aerodynamics showed that the shape of a wing has enormous effects on flight — but there is not just one "best" wing shape.
NewsGram brings to you top news around the world today.
The best shape in any moment depends on many factors: how much the aircraft weighs, the speed it is flying, and whether the pilot wants to climb higher or descend, for instance.
This means that a rigid wing with a limited number of moveable surfaces — also rigid — is only a compromise and cannot be the most efficient shape for the whole of any given flight.
The researchers explained that the shape-changing wing is constructed from building block units made of advanced carbon fibre composite materials.
Check out NewsGram for latest international news updates.
These building blocks are assembled into a lattice, or arrangement of repeating structures — the way that they are arranged determines how they flex.
The wing also features actuators and computers that make it morph and twist to achieve the desired wing shape during flight, the researchers said. (IANS)